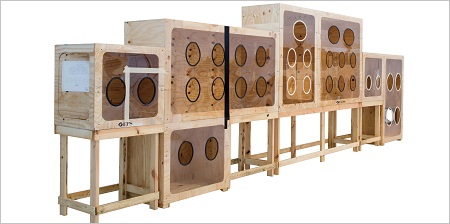
FPS Food and Pharma Systems è un’azienda italiana specializzata nella produzione d’impianti di micronizzazione e sistemi di contenimento per le aziende chimiche e farmaceutiche
L’esperienza maturata in 16 anni di attività consente ad FPS di essere un leader a livello mondiale, offrendo un servizio conforme agli elevati standard qualitativi per il mercato globale.
Il processo di progettazione e produzione degli impianti viene svolto interamente negli stabilimenti di Fiorenzuola d’Arda (PC), a partire da un attento ascolto delle richieste del cliente fino al test finale prima della consegna.
La capacità di ascolto e la flessibilità nell’adattarsi alle esigenze del cliente sono i punti di forza che negli anni hanno premiato FPS.
Lo studio iniziale del progetto avviene a più mani: un team specializzato lavora a stretto contatto con il cliente per assicurare il rispetto delle specifiche tecniche richieste.
Per quanto riguarda i sistemi di contenimento, FPS propone solitamente la costruzione di un simulacro (“mock-up”) dell’impianto oggetto di fornitura.
“Si tratta di una struttura che riproduce fedelmente in scala 1:1 il macchinario e fornisce un’idea visiva, quanto più dettagliata, di come sarà l’impianto finale. Le modalità di realizzazione del simulacro consentono al progettista ed al cliente di apportare facilmente durante la fase di verifica eventuali modifiche e miglioramenti” – spiega la dott.ssa Ilenia Lindi, responsabile dei Project Manager in FPS.
“Si esegue un mock-up per delineare gli aspetti ed alcuni dettagli che andranno a comporre la macchina finale, in modo da stabilire le posizioni ottimali di tutti i componenti, simulare le operazioni previste e sviscerare eventuali problematiche non discusse in fase di offerta. In ogni fase il cliente è supportato dal team di progetto, che coordinato dal Project Manager, lavora insieme al cliente per definire la migliore soluzione”.
Le fasi da considerare per eseguire il “mock-up” sono:
- Progettazione 3D dell’isolatore
- Disegno del mock-up
- Realizzazione del simulacro dell’isolatore
- Realizzazione dei componenti interni
- Realizzazione delle visive in policarbonato con il posizionamento delle flange guanto
Esecuzione della verifica di “mock-up” con il cliente e il team di progetto- Report finale con i dettagli dei riscontri evidenziati e delle soluzioni individuate
Prima di realizzare il simulacro, viene eseguito un attento studio preliminare della macchina, partendo dalla specifica di fornitura, considerando gli spazi a disposizione nel luogo d’installazione e la componentistica integrata all’interno della macchina (come macchine di processo o diverse tipologie di contenitori da manipolare). Il modello 3D dell’impianto è la base di partenza per la costruzione del simulacro.
Ai fini del raggiungimento del migliore risultato, è’ necessario simulare l’operatività completa che l’operatore eseguirà internamente all’isolatore; FPS provvede quindi a realizzare non solo il simulacro dell’impianto, ma anche i principali componenti interni su cui saranno eseguite le operazioni desiderate.
“A volte capita che, ancora in fase di offerta, il cliente non riconosca l’ importanza di questa fase, ritenuta “superflua” anche facendo leva sull’esperienza di FPS nella costruzione di sistemi di contenimento.
Quando tuttavia il suggerimento di FPS viene seguito e le persone vengono in azienda e toccano con mano quello che sarà la loro macchina, si “divertono a giocare” spostando i componenti e valutando soluzioni diverse rispetto a quelle che avevano inizialmente considerato. Una volta mi è capitato di accompagnare un cliente per un giorno intero in questo “gioco”, alla ricerca di soluzioni che riteneva migliori, per poi ritrovarmi a confermare la soluzione di partenza da noi proposta. Non ho comunque ritenuto che questo fosse stato tempo perso! È molto importante per noi che l’utilizzatore finale sia pienamente convinto di come verrà realizzata la soluzione finale e che lo sia nella configurazione migliore” – riprende Lindi.
“Trattandosi di sistemi complessi e che richiedono investimenti economici importanti, questo momento ci da l’opportunità di valutare, già in fase di progettazione, tutte le integrazioni che comportano extra costi ed eventuali riduzioni. Per esempio, ci è anche capitato di eliminare una camera di lavoro perché tutto il processo poteva essere svolto in una sola camera, a beneficio dei costi e degli ingombri dell’utente finale”.
Il grande vantaggio nella realizzazione di un simulacro è quello di lasciare che i veri utilizzatori finali eseguano le manipolazioni e “giochino” con la macchina e, quindi definiscano/visualizzino le operazioni per come effettivamente saranno.
“Per il test ergonomico di uno degli ultimi progetti – continua Lindi – un impianto molto complesso, era presente una vera delegazione: il project manager, il processista, il responsabile elettrico, l’operatore e alcuni tecnici della società di ingegneria che seguiva il progetto. Per 4 giorni abbiamo lavorato insieme alla verifica delle soluzioni proposte e ciascuno ha contribuito per la sua parte.
Non mi è mai capitato che un cliente rimanesse insoddisfatto dopo la verifica di un mock-up. Anzi, anche i più scettici ci hanno sempre riconosciuto l’utilità dell’attività svolta. Ad esempio, di recente abbiamo realizzato un isolatore simile ad uno già in funzione nella stessa azienda. Avremmo potuto “saltare” questa fase e riprodurre la macchina nello stesso modo. In accordo con il cliente invece, abbiamo investito una giornata di lavoro insieme per studiare un nuovo simulacro e valutare, in base alla loro esperienza, quali erano le migliorie da adottare per questa nuovo progetto”.
Anche dal punto di vista elettrico questo passaggio può dare vantaggi. Il responsabile del reparto elettrico ing. Luca Abbà spiega: “è vero che il simulacro è più utile per una valutazione ergonomica, meccanica e di spazi, ma anche dal punto di vista elettrico è molto vantaggioso. Per esempio, stiamo lavorando a stretto contatto con un cliente americano per proporre una soluzione adatta anche a questo mercato, che ha standard diversi da quelli europei”.
FPS crede molto in questo delicato passaggio poiché permette di avere un’idea molto fedele della macchina che poi sarà realizzata, di ottimizzare l’ergonomia e la logistica per il flusso dei componenti e di avere un risparmio in termini di costi e tempi da entrambe le parti.
“La realizzazione del simulacro ha un impatto di 2-3 settimane sullo sviluppo del progetto, che in caso di progetti con tempi stretti di realizzazione, possono essere un tempo importante” – racconta Gianola, Presidente e Direttore Commerciale. “Tuttavia, l’esperienza ci ha insegnato che investire nell’attività di mock-up consente di evitare problematiche in fase di installazione/commissioning e di utilizzo dell’impianto la cui risoluzione può richiedere molto più tempo.”
Come sempre, l’obiettivo di FPS è fornire un servizio all’industria chimica e farmaceutica. Il simulacro è uno degli strumenti che ci consentono di essere sempre più allineati con le aspettative dei nostri clienti.
Scheda Aziendale: FPS