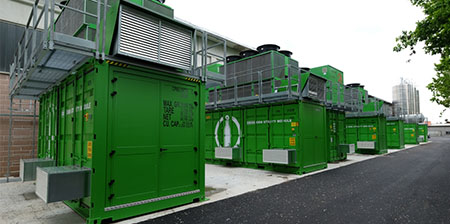
Serioplast, per il nuovo impianto di Pianiga, ha scelto i compressori Atlas Copco particolarmente compatti e alloggiati all’interno di container
Serioplast, azienda che produce imballaggi in plastica rigida per prodotti destinati all’igiene personale, alla pulizia della casa, al bucato e all’alimentazione, ha recentemente avviato il nuovo stabilimento di Pianiga, dedicato alla produzione di contenitori per il settore della detergenza. Per la produzione dell’aria compressa necessaria al processo produttivo sono utilizzati compressori d’aria Atlas Copco, scelti per la loro compattezza, per i bassi consumi energetici, e per la disponibilità del servizio di assistenza tecnica in tutto il mondo.
I compressori usati da Serioplast, infatti, devono essere installati in container dedicati all’aria compressa: si tratta di moduli standard, intercambiabili, facilmente trasportabili nei diversi stabilimenti.
Lo stabilimento di Pianiga, in provincia di Venezia, è in un’area industriale nei pressi dell’impianto dell’azienda cliente di Serioplast che realizza prodotti per il largo consumo. La strategia di espansione, infatti, prevede la costruzione di stabilimenti vicini ai siti di produzione del bene da confezionare per ridurre il costo del trasporto, che incide considerevolmente su un prodotto voluminoso e relativamente “povero” come i flaconi.
Questo è il motivo per cui l’azienda ha sviluppato il concetto di “Stabilimento Plug in and Play”, che consiste nell’ingegnerizzazione di container modulari dedicati alla produzione dei principali elementi che alimentano le linee produttive: resine, acqua, e aria compressa. A fronte della costruzione di un nuovo stabilimento è sufficiente posizionare all’esterno del capannone che ospita le macchine delle diverse linee produttive, uno o più moduli aria compressa. I moduli sono standard, intercambiabili, facilmente trasportabili, e affiancabili fra loro. In caso di espansione dello stabilimento è sufficiente aggiungere nuovi moduli. I vantaggi di questa soluzione sono la facilità di trasporto e di installazione, la scalabilità della struttura e la rapidità di avviamento, con tempi normalmente di 3-4 mesi da inizio installazione, aumentati a 4-6 mesi durante la pandemia.
Atlas Copco è riuscita a soddisfare il cliente nella realizzazione dei 4 container contenenti i compressori presenti a Pianiga: lo stabilimento è dedicato all’estrusione e al soffiaggio per la produzione di flaconi in polietilene ad alta densità (HDPE), in polipropilene (PP), e in polietilene tereftalato (PET) per il settore della detergenza. Il sito produttivo, che è dimensionato per la realizzazione di centinaia di milioni di flaconi all’anno, richiede oggi l’uso di quattro compressori alloggiati in altrettanti “moduli utilities” ingegnerizzati da Serioplast insieme ad un team di ingegneri specializzati di Atlas Copco.
Nello specifico i quattro moduli contengono rispettivamente tre compressori GA 110 a velocità fissa e un compressore GA 110 a velocità variabile, caratterizzati da uno stadio di compressione all’avanguardia e motore di classe IE5 raffreddato ad olio che richiede tempi di manutenzione ridotti abbattendo i tempi di fermo macchina. L’alloggiamento del motore completamente chiuso con grado di protezione IP66 garantisce la capacità di operare in modo affidabile nelle condizioni più difficili e a temperature ambiente fino a 55 °C / 131 °F. Per poter gestire i diversi compressori di uno stabilimento come un ‘unica rete di aria compressa è utilizzato il controller Atlas Copco Equalizer 4.0, che permette di risparmiare energia, ridurre la manutenzione e i tempi di inattività.
Michele Piccolo, progettista del reparto di ingegneria di Serioplast, che ha seguito il design del modulo, afferma: “Siamo molto soddisfatti della partnership con Atlas Copco, i cui progettisti ci hanno dato supporto per l’ingegnerizzazione, fornendo tutte le informazioni necessarie per la corretta integrazione del compressore nel nostro sistema containerizzato. Ogni modulo contiene tutti gli elementi fondamentali per la produzione di aria compressa: alimentazione, sistemi di filtrazione, gestione delle condense, sistemi di monitoraggio delle variabili di processo. È anche previsto lo spazio per permettere ai tecnici di intervenire ed è stato studiato un sistema di ventilazione interna affinché il sistema possa lavorare in diverse condizioni di temperatura esterna, da -15°C a + 45°C. Per un’azienda come la nostra, infine, è fondamentale la disponibilità di una rete di assistenza tecnica globale con customer center in ogni paese in cui è presente uno stabilimento.”
“I compressori della serie GA sono affidabili dal punto di vista tecnologico, hanno bassi consumi energetici e garantiscono tempi di fermo macchina ridotti, con conseguente riduzione dei costi produzione. Sono fondamentali da questo punto di vista il nuovo stadio di compressione, che garantisce un’efficienza del 7% maggiore rispetto alla serie precedente, e l’accesso semplice alle parti che necessitano una manutenzione più frequente”, afferma Elena Marazzi, Product Marketing Manager di Atlas Copco.
“Partecipare, insieme al cliente, all’ingegnerizzazione di un container dedicato all’aria compressa per la produzione di imballaggi in plastica rigida, progettato intorno al compressore è stata una sfida molto interessante”, afferma Davide Riva, Project Engineer di Atlas Copco, “Sono attualmente in fase di sviluppo quattro nuovi moduli che alloggeranno compressori GA110 e GA110VSD+ destinati all’Algeria e agli Stati Uniti”.